Corporate Social Responsibility
Education & Welfare Trust
Ghazi Education & Welfare Trust is a non profit welfare organization set up in 2003 to run charitable educational institutions in the historic and ancient city of Lahore. It was established with the sole purpose of imparting tuition free education to the poverty stricken yet talented and deserving children of the walled city and it’s surrounding areas.
Housing
Wall workers, regardless of designation or hiearchy, are provided with free housing. We have a fully maintained workers colony that consists of bachelor’s hostels, quarters, family apartments, executive accommodation and manager’s bungalows. A mini-market is also set up inside the colony to fulfill the everyday needs of all the workers.
Medical Care
We have established a medical clinic at the project to aid people suffering from minor ailments and illnesses. A registered medical practitioner maintains the clinic and essential medicines for minor ailments are available, free of charge, for our workers.
Subsidized Canteens
All the units have a subsidized canteen that provides good quality, affordable meals for the entire workforce. The management ensures the maintenance of the quality of food via random control measures to ensure consistency and upholding the hygenic standard of the food.
Social Activities
An Annual Workers Dinner is held in the green lawns of the project. All the workers are provided free Iftar (fast-breaking meal) and refreshing drinks during the holy month of Ramadan. Different types of Sports events, competitions and trips to recreational places continue to add color to the life at Ghazi Fabrics. Such measures and activities are held in order to foster and encouage the important attributes of teamwork and motivation. While at the same time it provides our employees with healthy extra cirricular activites to enage it.
BIOGAS
1) With natural gas prices on the rise, the management decided to experiment with the production of biogas in year 2010 and after various initial small scale tests with animal dung procured from neighboring villages, some positive results emerged. Thus it was decided to proceed with idea and gradually build our own cattle farm, leading to the construction of two Biogas Pits in the vacant land of Ghazi Power Ltd. In the first phase some twenty buffalos and two cows were brought in from the companies other farms which were scattered in various locations. After thoroughly research two pits were constructed by the end of the year. We were all set to start filling our digesters with a mixture of dung and water for the fermentation process to begin.
2) Our calculations based on our small scale tests indicated that typically 1 kg of cattle dung fed to a digester produced about 40 liters of biogas per day.
3) One cubic meter of biogas daily will produce the equivalent 2.5 to 3.5 stove hours.
4) One cow/buffalo produces about 8-10 kg dung per day.
5) By March 2011 we were in production and we had connected 10 kitchens within our factory premises with our very own in house biogas.
6) By mid 2011 we added two more pits and increased our animal population to 100.
7) At present we have 120 Cubic meter capacity per day and we are producing biogas which is equivalent to about Rs. 50,000/- of SNGPL. Furthermore the herd size has increased to a total of 134 animals.
8) Production of biogas varies in the summer and winter months, where our production in summers is about 20% more than in winters. This is due to the fact that during the winter months the cold temperature hampers the efficient fermentation of the dung.
Waste Heat Recovery
A waste heat recovery unit (WHRU) is an energy recovery heat exchanger that recovers heat from hot steams with potential high energy content, Such as hot flue gases from a gas/ diesel engine or steam from cooling towers or even waste water.
Waste Heat recovery boilers installed at Ghazi-
One duplex (connected with two engines exhaust) and one simplex (connected with one engine exhaust) were installed as soon as the gas power plant was commissioned. These boilers are locally manufactured and are capable of producing six tons of steam per hour when three engines are running on full load. With the installation of the boilers we not only increased our thermal efficiency by 20 % we also saved about Rs. 200,000 per day by not running our furnace oil boiler. These efforts have helped us advance our vision of being an environment friendly company which strives to make efforts in renewable energy initiatives.
Fire Fighting
Our mills are equipped with a variety of fire fighting methods. We have 11 fully trained fire fighters who man the fire station in rotating shifts. Furthermore they are equipped with essential items such as fire suits and face masks which are replaced whenever the need arises. The premises are also equipped with over 182 fire extinguishers of different types (Co2, foam, etc) for combating fire related incidents. Furthermore drills are conducted on an annual basis to make sure all employees are familiar with the employee evacuation procedures.
Earth Quake Relief
GFI has always risen to the occasion whenever Pakistan has been in the midst of testing times. In 2005 a major earthquake struck various parts of the country with the nothern parts of the country being the worst affected. Contribution towards the earthquake relief effort from the civil society of Pakistan was very generous and admirable. Keeping our national and civic duty in mind GFI immediately mobilized essential equipment as well as rations etc. for the earthquake refugees. GFI was among one of the most the most significant contributors from the corporate sector to the relief effort of affected people.
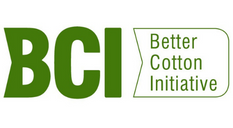
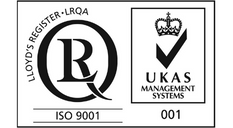
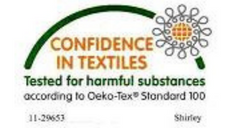
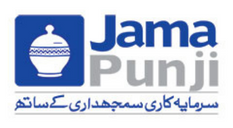
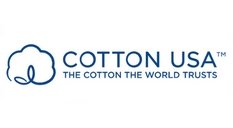