Quality Assurance
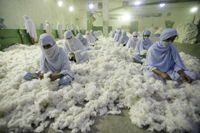
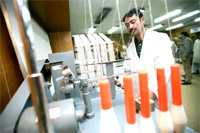
Workers are given monetary rewards at the end of each month based on their performance. This drives workers to pick at maximum visible contamination, thereby having a positive impact on yarn quality.
One worker picks out contamination from only one bale of cotton per day and not more. We strictly adhere to this standard to ensure maximum worker focus and effective picking of contamination from a bale of cotton.
RIETER B-11 cleaning points are installed in the Blow Rooms of both the units. It ensures maximum fiber cleaning, trash removal and maximum security of fiber during beating.
RIETER Finisher Draw frames help to control CV% of count and to ensure proper leveling and blending of sliver to produce an even and homogeneous yarn. This further helps us maintain a consistent quality level.
In pursuance of our BMR (Balancing, Modernization and Replacement) programme, SCHLAFHORST SCH-338 winders have been installed with LOEPFE 800i and 900i yarn cleaners and contamination channels. These splice out and eliminate any residual yarn faults. Ultimately, we will replace all our older machines with the latest ones.
Quality Control laboratory
We have state of the art Quality Control laboratory with the following equipment:
- Uster Tester
- Uster Tensorapid
- Uster Auto Sorter
- Classimate
- Fibrograph
- Micronair
- Stelometer
Customer Service
This is the most important part of Quality Assurance that most people do not take into consideration. This particular aspect begins when our product, yarn or fabric, enters the premises of our customer. Our technical staff personally visits the customer to ensure smooth running of our product. It also ensures that the customer is well satisfied by the performance of our product.
Therefore, the Quality Journey does not end within the four walls of our mills. It goes beyond our physical boundaries, and beyond the expectations of our customers!
Mixing is the first step in quality assurance process. In mixing department we have a dedicated workforce of female workers. The ladies are split up into three lines to hand-pick visible contamination from cotton. Workers are given monetary reward at the end of each month based on their performance. This drives workers to pick out visible contamination, thereby assuring yarn quality.
Loptex and Rieter B-11 cleaning points are installed in Blow Room of both the units. It ensures maximum fiber cleaning, trash removal and maximum se curity of fiber during beating for homogeneous yarn. This further helps us to maintain quality level. This particular aspect begins when our product, yarn or fabric enters the premises of our customer. Our technical staff personally visits the customer to ensure that the customer is well satisfied by the performance of products.
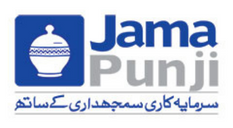
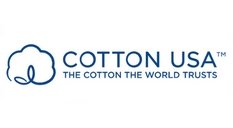